What You Need to Know About Prefabricated Construction for Your Next Build
When considering your next construction project, prefabricated construction is a superior approach that involves manufacturing building components in a controlled factory environment. This method considerably reduces project timelines by up to 50%, as site preparation and factory fabrication can occur simultaneously, minimizing weather-related delays. It enhances quality and safety through stringent quality checks and controlled conditions, reducing on-site labor risks. Prefabrication also promotes sustainability by reducing material waste and employing environmentally friendly practices. Additionally, it offers substantial cost savings by lowering labor and material costs. By adopting prefabrication, you can achieve faster, safer, and more sustainable construction, and continuing to explore this topic will reveal more of its benefits and implementation strategies.
Introduction to Prefabricated Construction
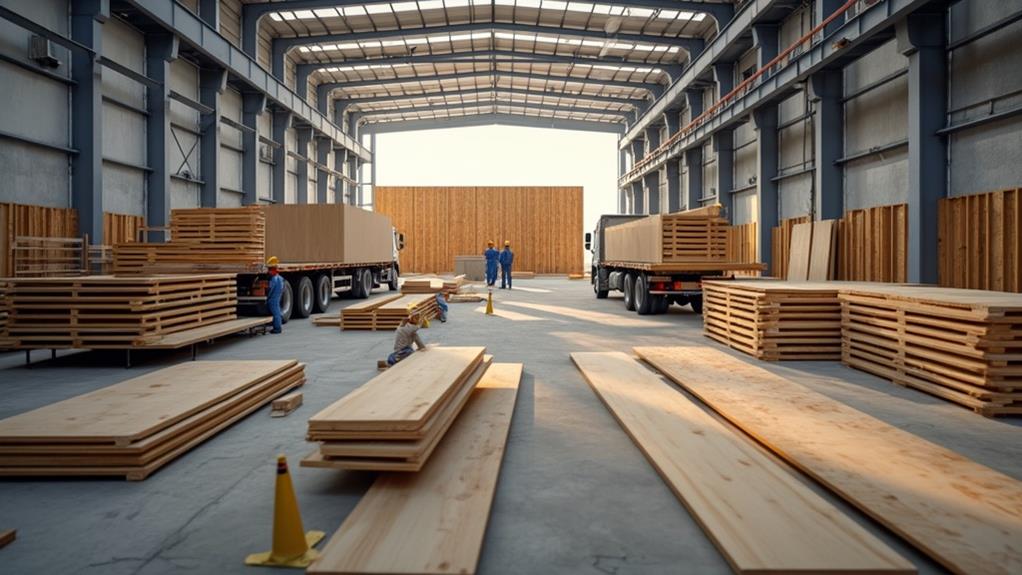
Prefabricated construction involves manufacturing building components in a controlled factory environment, which are then transported to the construction site for assembly. This method differs markedly from traditional on-site construction, where components are built from scratch at the job site, often exposed to weather conditions and other environmental factors. By streamlining the manufacturing and assembly process in a factory setting, prefabricated construction reduces project timelines, minimizes material waste, and guarantees higher quality control and safety standards.
What is Prefabricated Construction?
Prefabricated construction represents a transformative approach in the building industry, characterized by the manufacture of building components in a controlled factory environment, away from the actual construction site. This method involves producing and assembling various parts of a building, such as walls, floors, and roofs, under stringent quality control measures before transporting them to the site for final assembly.
Here are three key aspects of prefabricated construction:
1. Time Efficiency
Prefabricated construction remarkably reduces project timelines by allowing site preparation and factory fabrication to occur simultaneously. This overlap minimizes delays caused by weather conditions and accelerates the construction schedule, enabling projects to be completed up to 50% faster than traditional construction methods[1][2][4].
2. Sustainability in Construction
Prefabrication is more eco-friendly compared to traditional construction. It reduces material waste by utilizing extra materials for recycling and repurposing, and it employs environmentally friendly materials. The controlled factory environment also enhances air filtration and wall insulation, increasing energy efficiency and reducing the overall carbon footprint[1][2][4].
3. Quality and Safety
Manufacturing components in a factory guarantees higher quality and consistency. Quality checks are conducted before the components are dispatched, ensuring they meet safety regulations and quality standards. This approach also reduces on-site labor, minimizing the risk of accidents and exposure to hazardous conditions[2][3][4].
Key Differences Between Prefabricated and Traditional Construction
When comparing prefabricated construction to traditional methods, several key differences emerge that highlight the innovative advantages of prefabrication.
Construction Speed
Prefabricated construction markedly reduces build times. While traditional construction can take 6-16 months, prefabricated methods can be completed in as little as 6-8 weeks. This is because prefabricated components are manufactured offsite in controlled factory environments, allowing for simultaneous preparation of the construction site[1][5].
Design and Customization
Prefabrication, particularly modular construction, offers a balance between design constraints and modern aesthetics. Although modular builds may have some design limitations, they can be combined with traditional elements for a contemporary look. Traditional construction, on the other hand, allows for more granular customization but often involves a longer and more complex design process[1][5].
Cost Savings and Sustainability
Prefabrication is associated with cost savings due to reduced material waste and labor costs. The use of sustainable building materials and efficient production processes in factories also minimizes environmental impact. Here is a summary of the key differences:
Aspect | Prefabricated Construction | Traditional Construction |
---|---|---|
Construction Speed | 6-8 weeks | 6-16 months |
Design Flexibility | Balanced, modern aesthetics | Highly customizable, complex design process |
Cost and Sustainability | Reduced material waste, lower labor costs, sustainable materials | Higher material waste, variable labor costs, more environmental impact |
Prefabrication stands out for its efficiency, cost savings, and commitment to sustainable building practices, making it an attractive option for various construction projects[1][4][5].
Benefits of Prefabricated Construction
When you adopt prefabricated construction, you can considerably reduce project timelines and costs. By manufacturing building components in a controlled factory environment, you guarantee high-quality outputs with precise specifications and minimal waste, which also enhances sustainability. This method is versatile, applying efficiently to residential, commercial, and agricultural projects, allowing for customizable and environmentally friendly builds.
Time Efficiency and Cost Savings
In the pursuit of streamlined construction processes, one of the most notable advantages of prefabricated construction is its ability to drastically reduce project timelines and associated costs. This method, often referred to as panelized construction, involves manufacturing building components in a controlled factory environment, which are then assembled on-site. This approach is particularly beneficial in residential prefabrication, where it can speed up construction by as much as 50% and cut costs by 20%[1][3][4].
Here are three key ways prefabricated construction achieves time efficiency and cost savings:
- Accelerated Construction Schedules: Prefabricated components can be manufactured concurrently with on-site work, such as site preparation and foundation laying. This parallel workflow markedly reduces the overall project timeline[1][3][5].
- Reduced Labor Costs and Site Overhead: By moving a considerable portion of the labor activity off-site to a controlled manufacturing facility, costs associated with on-site labor, supervision, and temporary facilities are lowered. This can reduce labor costs by up to 80% in some cases[4].
- Minimized Waste and Rework: The precise and controlled factory environment assures that prefabricated components are made to exact specifications, reducing the need for on-site adjustments and rework. This also minimizes waste generation, further contributing to cost savings[2][3][4].
These efficiencies in prefabricated construction not only save time and money but also enhance the overall quality and sustainability of the build.
Enhanced Quality and Sustainability
Prefabricated construction not only streamlines project timelines and reduces costs but also greatly enhances the quality and sustainability of the final build. When you opt for prefabricated construction, you benefit from a controlled factory environment where every component is meticulously engineered and produced.
Here are three key ways prefabrication improves quality and sustainability:
Enhanced Quality Control
- Prefabricated components are manufactured in a controlled environment, guaranteeing consistent quality through standardized processes and stringent quality checks. This method minimizes the risks associated with varying skill levels among on-site workers and the impact of weather conditions, resulting in structurally sound and aesthetically pleasing buildings[1][4][5].
Sustainable Materials and Practices
- Prefabrication often incorporates eco-friendly materials such as cross-laminated timber (CLT), which is durable and sustainably sourced. The factory setting allows for precise material usage, reducing waste and the environmental impact of construction. Materials are recycled or repurposed, aligning with modern environmental standards[3][4][5].
Advanced Technology Integration
- Companies like Twin Maple Construction leverage technologies such as Building Information Modeling (BIM) to enhance the precision and efficiency of prefabricated construction. BIM allows for detailed planning and visualization, reducing errors and guaranteeing that every component meets the highest standards before being transported to the site[2][5]. This integrated approach guarantees a high-quality, sustainable, and efficient building process.
Applications in Various Sectors
When considering the applications of prefabricated construction, you can see its benefits across various sectors. In residential projects, prefabrication allows for speedy construction of high-quality homes with minimal on-site labor, reducing costs and environmental impact[1][3][5]. For commercial projects, it enables the swift assembly of complex structures, enhancing efficiency and precision, while in agricultural projects, it provides durable and customizable solutions that can withstand harsh environmental conditions[1][3][5].
Residential Projects
In residential projects, embracing prefabricated construction can considerably enhance the building process, offering numerous benefits that cater to the unique needs of homeowners. Prefabrication guarantees precise building information modeling (BIM) and controlled factory environments, similar to commercial prefabrication, to deliver high-quality components. This method also enables off-grid prefabricated solutions, reducing construction time and environmental impact while providing durable, low-maintenance homes.
Commercial Projects
Moving from the precision and efficiency seen in residential projects, commercial construction also stands to benefit considerably from prefabricated methods. Commercial projects can leverage prefabrication to accelerate construction timelines, enhance quality, and minimize waste. Using Building Information Modeling (BIM) and meticulous design and logistics planning, you can guarantee seamless integration of components, even for complex projects, similar to those in agricultural buildings. This approach reduces risks, improves safety, and lowers costs, making it an ideal choice for commercial builds.
Agricultural Projects
Prefabricated construction offers significant benefits for agricultural projects, enhancing efficiency, safety, and sustainability in farm and ranch settings. By utilizing prefabricated components, farmers can optimize storage space, improve ventilation, and guarantee consistent temperatures. Building Information Modeling (BIM) and hybrid construction models enable precise planning and execution, reducing material waste and on-site labor. This approach also minimizes environmental impact and enhances the overall durability of the structures.
Challenges in Prefabricated Construction
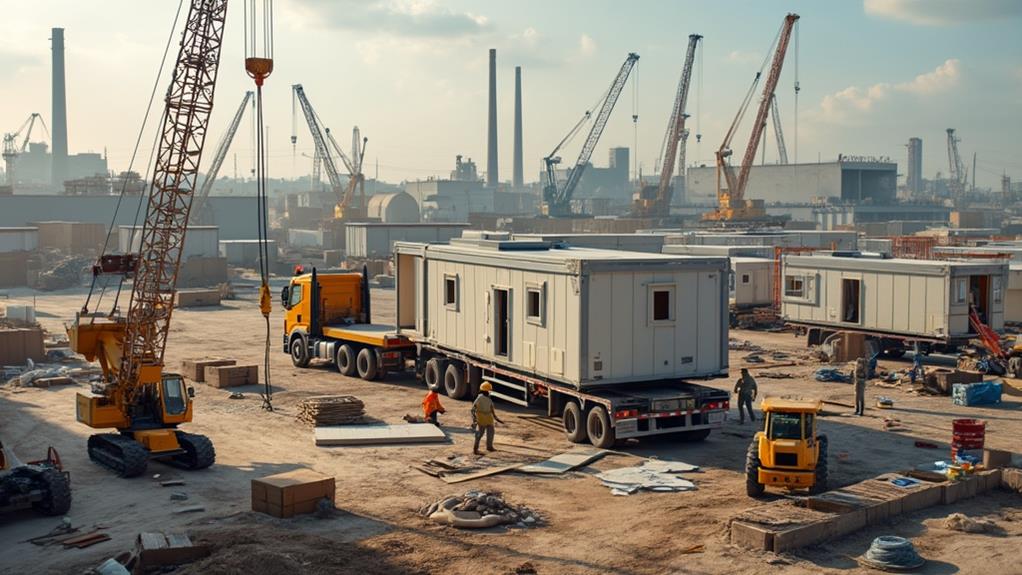
When engaging in prefabricated construction, you must navigate the complexities of transportation and site adjustments, as modules fabricated in a factory need to be carefully transported to the site without damage. This involves evaluating logistical constraints such as road conditions, bridge clearances, and site access to guarantee the modules can be safely delivered and placed. Additionally, you will need to address design and perception constraints, as the modular approach can limit design flexibility and may require more upfront planning and design decisions to guarantee all modules fit together seamlessly.
Transportation and Site Adjustments
Transporting prefabricated construction components presents several significant challenges that can greatly impact the efficiency and cost of a project. One of the primary concerns is the logistical complexity of moving oversized and heavy modules. For instance, volumetric modules often exceed standard road dimensions, requiring specialized trailers, escort vehicles, and additional permits. This can lead to increased costs and the need for careful route planning to avoid narrow roads, bridges, and tunnels that may not accommodate these large loads[2][3][4].
To mitigate these challenges, it is important to engage in meticulous planning and coordination. Utilizing building information modeling (BIM) can help in optimizing module design and identifying potential transportation hurdles early in the project. This guarantees that the modules are designed to fit together seamlessly and can be transported safely. Additionally, working with experienced logistics specialists is essential for securing the right equipment, guaranteeing proper module securing, and predicting and managing potential delays due to weather or road conditions[2][4].
On-site adjustments also play a significant role in prefabricated construction. Confirming that the site is prepared to receive and assemble the prefabricated components efficiently is critical. This includes having the necessary lifting equipment, staging areas, and a well-coordinated installation plan to avoid congestion and delays. By addressing these transportation and site adjustments proactively, you can guarantee a smooth and efficient prefabricated construction process.
Addressing Design and Perception Constraints
In the domain of modular construction, several design and perception constraints can greatly impact the efficacy and appeal of prefabricated buildings. These constraints often revolve around the limitations inherent in the prefabrication process and the need for innovative solutions to overcome them.
Design Limitations
- Dimensional Restrictions: Modules must be designed to fit within transportation regulations, which can limit architectural creativity and flexibility. For instance, modules cannot exceed the dimensions of a standard shipping container, restricting the design of larger or more complex structures[5].
- Material Choices: While materials like cross-laminated timber (CLT) offer excellent structural integrity and sustainability, they must be carefully selected to guarantee they meet both design specifications and transportation requirements. CLT, for example, can be used to create large, yet transportable, modules due to its lightweight and strong properties[3].
- Integration Complexity: The use of Building Information Modeling (BIM) is essential in modular construction to guarantee that all modules fit together seamlessly. However, integrating these modules with traditional construction methods can be complex, requiring meticulous planning and coordination. Robotics in construction can also aid in this process by automating the assembly and guaranteeing precise alignment of the modules[4][5].
Addressing these design constraints involves a thorough front-loaded design process, where architects, engineers, and contractors must work closely together to guarantee that all elements of the project align perfectly. By leveraging advanced technologies and innovative materials, the limitations of modular construction can be mitigated, leading to efficient, customizable, and environmentally friendly builds.
Best Practices for Implementing Prefabrication
To implement prefabrication effectively, you must integrate it early in the project design phase, guaranteeing that all stakeholders, including architects, engineers, and contractors, are aligned from the outset. Collaborating with experienced providers is vital, as they can offer specialized knowledge and resources to optimize the prefabrication process. Proper site preparation and logistics management are also essential, involving detailed planning and real-time tracking to confirm that prefabricated components arrive just in time for assembly, minimizing delays and rework[1][3][4].
Early Integration in Project Design
When starting on a prefabricated construction project, early integration in the design phase is essential for guaranteeing a seamless and efficient process. This involves collaborating closely with all stakeholders, including architects, engineers, manufacturers, and contractors, from the very outset.
To achieve this, here are some key practices to follow:
Early Integration Steps
- Utilize Building Information Modeling (BIM): Implement BIM to guarantee that all parties are synchronized with the latest design plans. This enhances accuracy, reduces mistakes, and allows for real-time updates and changes[1][3][5].
- Select Appropriate Materials: Consider materials like cross-laminated timber (CLT) that are well-suited for prefabrication. CLT offers advantages regarding speed, quality, and sustainability, which are particularly beneficial in regions like British Columbia’s Fraser Valley[3][5].
- Define Project Goals and Requirements: Clearly outline the project’s objectives, including timelines, budget, and specific client needs. This helps in evaluating the project’s suitability for prefabrication and in developing a thorough project plan[2][3].
Collaboration with Experienced Providers
Collaborating with experienced providers is pivotal for the successful implementation of prefabricated construction. This approach guarantees that all stakeholders, including architects, engineers, manufacturers, contractors, and suppliers, are aligned and working towards the same goals from the early stages of the project.
Effective collaboration requires several key practices:
Best Practices for Collaboration
- Early Planning and Integrated Design: Engage with designers, engineers, and manufacturers early in the project to guarantee building plans are suitable for modular techniques. This integrated design approach helps in optimizing efficiency and achieving project goals[2][3][4].
- Seamless Communication and Coordination: Utilize digital tools such as Building Information Modeling (BIM) software to automate workflows, deliver real-time data, and facilitate communication among project partners. This helps in sequencing the design-to-fabrication workflow and detecting potential clashes early[3][5].
- Clear Roles and Leadership: Assign leadership roles to guarantee the project stays on track. Select team members based on the value they bring to the project, not just their bid price. This ensures that the project benefits from the expertise of all team members, leading to better financial outcomes and higher quality results[5].
Site Preparation and Logistics Management
Efficient site preparation and logistics management are essential elements in the successful implementation of prefabricated construction. Before the arrival of prefabricated components, you need to establish clear construction site boundaries. This involves marking and staking the area using temporary fencing to define the work site and guarantee everyone is aware of the space requirements[1].
Soil tests and ground scans are critical next steps. Soil tests determine the soil’s composition to confirm it can support the building’s foundation and withstand construction activities like excavation and concrete pouring. Ground scans, conducted by an environmental engineer, help locate unmarked utilities and potential hazards beneath the surface, which are then marked for visibility[1].
Creating a traffic management plan is also essential to confirm safe movement of vehicles and pedestrians around the site. This plan should include strategies to separate people and construction vehicles, minimize vehicle movement, and enhance visibility for all parties involved[1].
Additionally, designate a materials storage area that is level, well-drained, and easily accessible. This area should be protected to prevent damage to the materials and modular units, guaranteeing a smooth assembly process when the time comes[1].
Twin Maple Construction’s Expertise
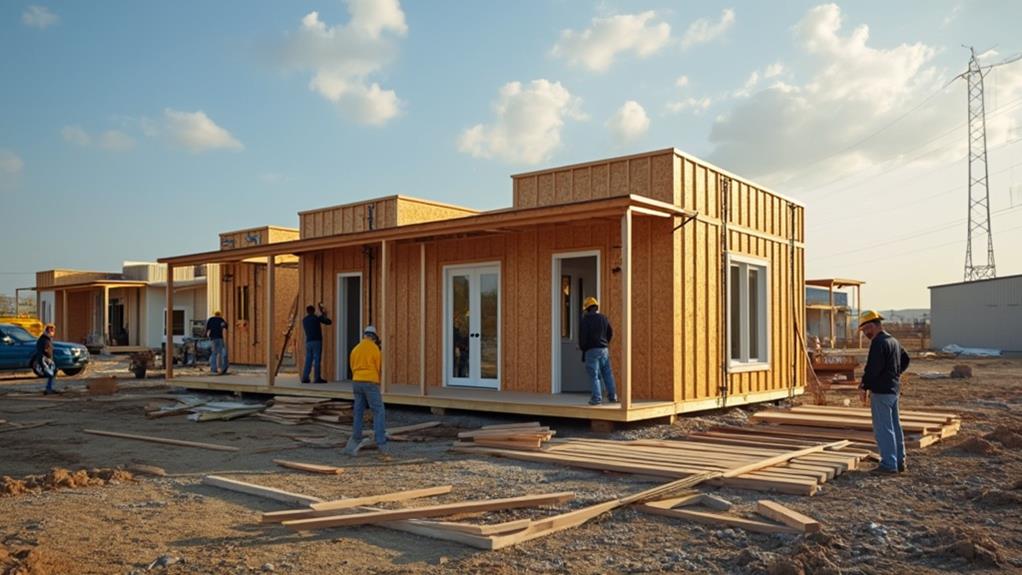
When working with Twin Maple Construction in British Columbia’s Fraser Valley, you benefit from their local knowledge and commitment to sustainable practices, which are integral to their prefabricated construction projects. The company guarantees quality and precision by manufacturing building components in a controlled factory environment, resulting in high-quality and customizable builds. Notable projects, such as their free-range organic chicken barns and commercial tenant improvements, showcase their expertise in delivering efficient and environmentally friendly solutions.
Local Knowledge and Sustainable Practices
Twin Maple Construction’s expertise in local knowledge and sustainable practices is rooted in their commitment to operating ethically and sustainably, guided by uncompromising principles. This approach is evident in their construction techniques, which prioritize environmental stewardship and community values. By leveraging local knowledge, they can tailor projects to the specific needs and conditions of British Columbia’s Fraser Valley, ensuring that each build is both efficient and environmentally friendly.
Their sustainable practices include the use of prefabricated components, which reduce waste and minimize the environmental impact of construction sites. This method also allows for precise control over material usage, leading to higher quality and more durable builds. Twin Maple Construction’s commitment to sustainability extends to their choice of materials and resources, often selecting local and eco-friendly options to support the local economy and reduce carbon footprint.
In addition, their ethical operations involve continuous planning and innovation to improve sustainability standards. This includes adopting advanced construction technologies and methodologies that enhance energy efficiency and reduce environmental harm. By integrating local knowledge with sustainable practices, Twin Maple Construction delivers projects that not only meet but exceed client expectations while contributing positively to the community and environment.
Quality and Precision in Prefabricated Projects
In the domain of prefabricated construction, quality and precision are paramount, and Twin Maple Construction excels in these aspects. When you choose prefabricated construction, you are opting for a method that guarantees high-quality outcomes through controlled and precise manufacturing processes.
Here are three key ways Twin Maple Construction maintains quality and precision in prefabricated projects:
Controlled Environment
- Prefabricated components are manufactured in a controlled factory environment, which minimizes the impact of weather conditions and other external factors that can compromise quality. This setting allows for consistent and high-standard production.
Advanced Technology and Tools
- Twin Maple Construction leverages advanced technologies such as Building Information Modeling (BIM) and digital tools to streamline the design and construction process. These tools enhance collaboration, reduce errors, and guarantee that every component meets precise specifications.
Rigorous Quality Control
- Each prefabricated component undergoes rigorous quality control checks before being transported to the site. This guarantees that every part of the structure meets the highest standards, resulting in a final product that is both durable and aesthetically pleasing.
Notable Prefabricated Projects in the Fraser Valley
In the Fraser Valley, several notable projects showcase Twin Maple Construction’s expertise in prefabricated construction. One of the standout examples is their work on agricultural projects, such as the Free Range Organic Chicken Barn. This project involved the prefabrication of barn components in a controlled factory environment, which were then efficiently assembled on-site. This method guaranteed high-quality construction, reduced timelines, and maintained strict environmental standards.
Twin Maple Construction has also applied prefabrication techniques in commercial projects, like the Kirmac Collision and Fountain Tire buildings. These projects highlight the company’s ability to deliver customizable, efficient, and sustainable builds. By manufacturing components in a factory, they can maintain precise quality control, minimize site disruptions, and adhere to strict deadlines.
Their approach to tenant improvement projects further underscores their expertise. Twin Maple Construction collaborates closely with clients to design and prefabricate components that meet specific needs, making certain that the final product is both functional and aesthetically pleasing. This methodological and innovative approach has earned them a reputation for delivering projects on time and on budget, making them a trusted name in the Fraser Valley’s construction industry.
Future Trends in Prefabricated Construction
As you explore the future of prefabricated construction, you’ll notice a significant shift towards sustainable and hybrid models, where prefabricated buildings are designed with eco-friendly materials and energy-efficient features. Advancements in materials and automation, such as the integration of 3D printing and robotics, will further enhance the efficiency and quality of prefabricated components. Additionally, prefabrication will play a vital role in off-grid and emergency solutions, providing rapid and reliable construction options for remote or disaster-stricken areas[2][3][5].
Adoption in Sustainable and Hybrid Models
The adoption of prefabricated construction in sustainable and hybrid models is driven by the escalating need for environmentally conscious and efficient building practices. Companies like Plant Prefab are at the forefront of this movement, utilizing a hybrid modular model that combines 2D panels with 3D modules. This approach minimizes onsite waste and disruptions, reducing the environmental impact of construction. Plant Prefab’s system produces 30% less construction waste than traditional site-based methods and has achieved carbon-neutral operations since 2020[2].
Hybrid modular construction integrates the adaptability of 2D panelised construction with the efficiency of 3D modules, offering a versatile and sustainable solution. This method optimizes material usage, incorporates energy-efficient technologies, and utilizes eco-friendly materials. The precision of offsite manufacturing reduces transportation-related emissions and enhances overall building energy performance, aligning with sustainability goals[3].
This innovative approach also streamlines the construction process, compressing schedules and eliminating material waste. Plant Prefab’s use of digital twin preconstruction builds empowers the company to elevate the quality of structures and systems, making sustainable housing more attainable and efficient. This model is set to expand, serving broader regions and contributing to the reduction of the ecological footprint of construction projects[2].
Advancements in Materials and Automation
Prefabricated construction is poised to leverage cutting-edge advancements in materials and automation, further enhancing its efficiency, quality, and sustainability.
Advancements in Materials
New materials are being integrated into prefabrication to enhance sustainability and performance. For instance, the use of cross-laminated timber (CLT) and sustainably sourced timber reduces waste and environmental impact[1][5].
- Eco-friendly Materials: Recycled steel, sustainable timber, and prefabricated concrete solar panels are becoming more common, aligning with environmental responsibility and innovation.
- Energy Efficiency: Advanced insulation materials and energy-efficient systems are incorporated to minimize energy consumption.
Advancements in Automation
Automation is revolutionizing the prefabrication process, making it more efficient and precise.
Automation Technology | Benefits |
---|---|
Building Information Modelling (BIM) | Facilitates collaborative planning, designing, and management; enhances visibility and issue resolution[1][2] |
Robotics and Automation | Streamlines component creation, improves precision, and reduces labor risks; examples include robotic bricklaying systems[1][3] |
3D Printing | Allows for complex component creation using new materials, pushing design and functionality boundaries[5] |
Artificial Intelligence (AI) | Undertakes complex tasks, optimizes workflows, and enhances overall efficiency[2][5] |
These advancements guarantee that prefabricated components are produced with high accuracy, speed, and quality, making the construction process more cost-effective and sustainable.
Off-Grid and Emergency Solutions
Embracing the future of prefabricated construction, off-grid and emergency solutions are becoming increasingly essential, especially in areas with limited infrastructure or those prone to natural disasters. These solutions leverage the efficiency and versatility of prefabricated construction to provide rapid, reliable, and sustainable housing and power options.
For off-grid applications, prefabricated construction allows for the integration of renewable energy systems, such as solar and wind power, along with advanced battery storage. This combination enables homes and facilities to be self-sufficient, reducing reliance on external utilities.
Here are three key benefits of prefabricated off-grid and emergency solutions:
Rapid Deployment
Prefabricated modules can be quickly transported and assembled on-site, providing immediate shelter and power in emergency situations. This is particularly vital in disaster zones where time is of the essence[2][3].
Scalable and Flexible
Modular designs can be easily scaled up or down depending on the needs of the project. This flexibility also allows for the adaptation of structures to various environmental conditions, ensuring they remain resilient in extreme weather[1][3].
Sustainable and Efficient
Prefabricated construction incorporates clean technology and sustainable materials, reducing the environmental impact of the build. Integrated systems for water harvesting and treatment, along with energy-efficient designs, make these solutions highly sustainable and efficient[3][5].
Conclusion and Call to Action
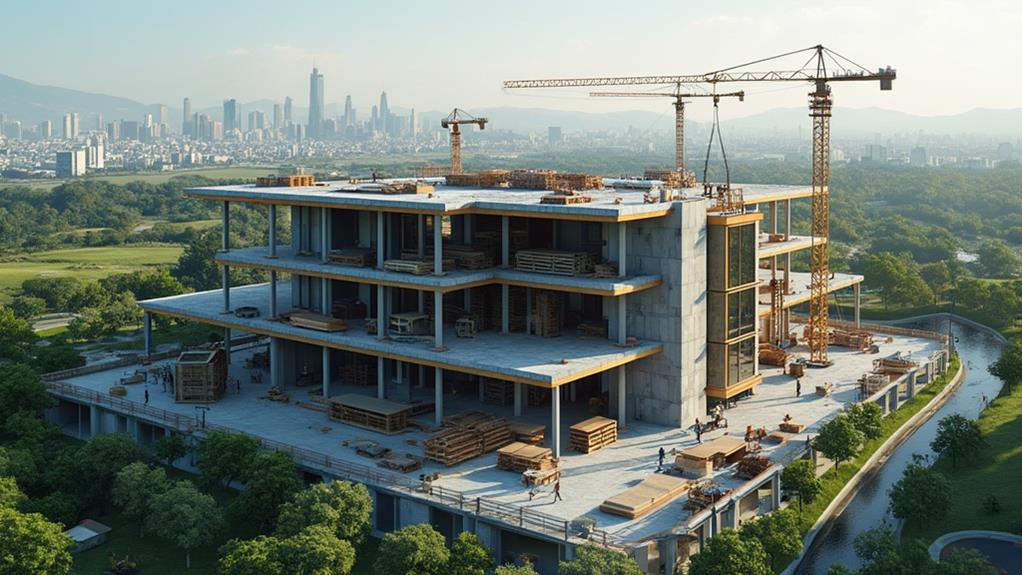
When considering prefabricated construction projects, you should choose Twin Maple Construction for their expertise in delivering efficient, customizable, and environmentally friendly builds. Based in British Columbia’s Fraser Valley, Twin Maple Construction specializes in commercial, agricultural, and tenant improvement projects, ensuring high-quality outcomes through controlled factory manufacturing and swift on-site assembly. Their track record of completing projects on time and on budget makes them an ideal partner for your prefabricated construction needs.
Why Choose Twin Maple Construction for Prefabricated Projects?
Choosing Twin Maple Construction for your prefabricated project means leveraging a methodology that masterfully combines efficiency, quality, and sustainability. By opting for prefabricated construction, you benefit from a process that occurs in a controlled factory environment, shielding the building components from weather-related delays and guaranteeing consistent quality. This method greatly reduces construction timelines, often by 40 to 50% compared to conventional construction, as the factory work can proceed simultaneously with site preparation.
Twin Maple Construction’s expertise in prefabrication translates into cost savings, as quicker project completion reduces labor costs and minimizes on-site disruptions. The controlled environment also enhances safety, eliminating many hazards associated with traditional construction sites. Additionally, prefabricated construction is more environmentally friendly, with reduced material waste and the efficient use of resources.
Twin Maple Construction tailors their prefabricated solutions to meet your specific needs, whether it’s for residential, commercial, or agricultural projects. Their approach guarantees high-quality structures with minimal long-term maintenance, enhanced durability, and improved energy efficiency. By choosing Twin Maple, you are investing in a sustainable, efficient, and customizable building solution that aligns with your vision and values.